A K24 crankshaft is a crankshaft that is used in some Honda K-series engines. The K-series engines are a family of inline-four engines that were designed and produced by Honda. The K24 crankshaft is used in the larger displacement K-series engines and has a stroke length of 86.0mm.
A K20 block is the part of an engine that houses the cylinders, pistons, and other internal components. It is called a “block” because it is typically made from a single block of metal. The K20 block is used in the Honda K-series engines and is designed for use with the smaller displacement K-series engines.
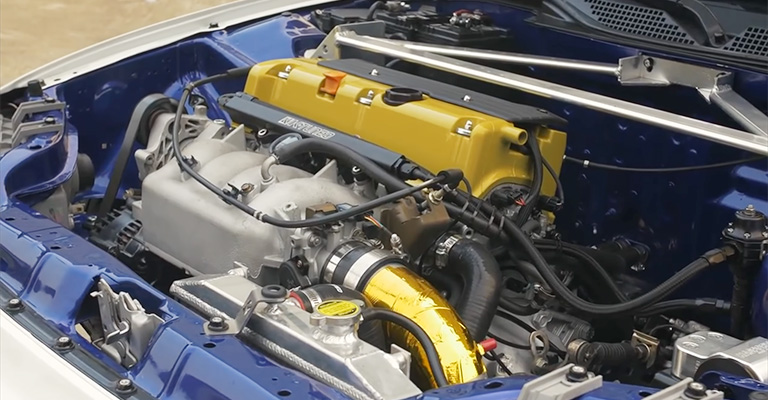
Can I Use K24 Crankshaft in K20?
It is possible to use a K24 crank in K20 block, but it will require custom pistons and rods to work properly. The K24 crankshaft is longer than the K20 crankshaft and has a different stroke, so the pistons and rods will need to be modified to fit the new crankshaft.
This will likely require the services of a machinist or engine builder who has experience with this type of modification.
Additionally, the K24 crankshaft may require some modification to fit in the K20 block.
It is also worth noting that this modification will significantly alter the engine’s displacement and may require other supporting modifications, such as a different intake manifold, fuel system, and possibly even a different engine management system.
As such, it is important to do thorough research and consider the costs and potential benefits before proceeding with this modification.
Pros and Cons of Using K24 Crankshaft in a K20 Block
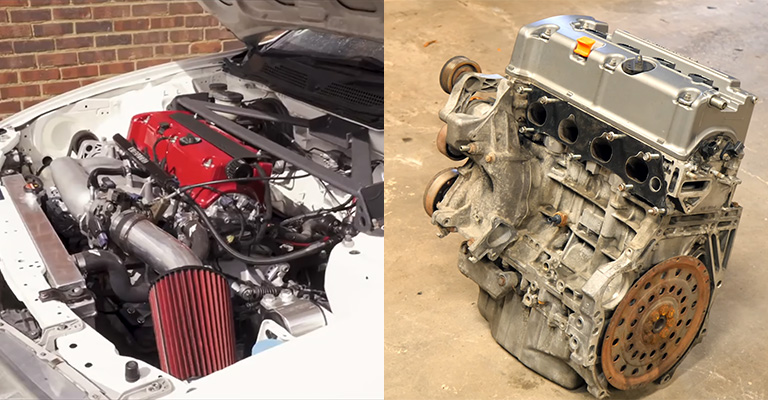
Some potential pros of using a K24 crankshaft in a K20 block could include:
- Increased displacement: The K24 crankshaft has a longer stroke than the K20 crankshaft, which will increase the engine’s displacement and potentially allow for more power to be produced.
- More torque: The increased displacement of the engine may also result in more torque being available at lower RPMs.
- Availability: K24 crankshafts may be easier to find or less expensive than other options for increasing displacement.
Some potential cons of using a K24 crankshaft in a K20 block could include:
- Complexity: The modification requires custom pistons and rods, which will likely need to be machined to fit the new crankshaft. This can be a time-consuming and costly process.
- Reduced reliability: The modification may result in increased strain on the engine and could potentially reduce its reliability.
- Reduced revving ability: The longer stroke of the K24 crankshaft may result in a reduction in the engine’s maximum RPM potential.
- Compatibility issues: The modification may require other supporting modifications, such as a different intake manifold, fuel system, and possibly even a different engine management system.
It is important to carefully consider all of these potential pros and cons before deciding to proceed with this modification.
How to Replace K24 Crank In K20 Block?
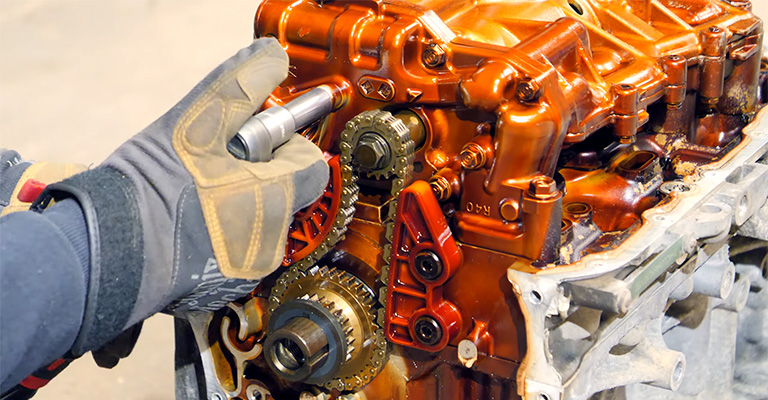
Here is a general outline of the steps that may be involved in replacing a K24 crankshaft in a K20 block:
- Gather the necessary tools and materials. This will likely include a hydraulic press, crank turning tool, dial indicator, micrometer, and other specialized tools. You will also need custom pistons and rods to fit the K24 crankshaft.
- Remove the old crankshaft from the engine. This will typically involve removing the oil pan, main bearings, and connecting rods. You may also need to remove the timing chain or belt and any other components that are in the way.
- Clean and inspect the engine block. Be sure to thoroughly clean the block and inspect it for any damage or wear. Any issues should be addressed before installing the new crankshaft.
- Press the new custom pistons onto the connecting rods. This will typically involve using a hydraulic press to press the pistons onto the rods, being careful to align them properly.
- Install the new custom rods onto the crankshaft. This will typically involve sliding the rods onto the crankshaft and securing them in place with rod bolts.
- Install the K24 crankshaft into the engine block. This will typically involve aligning the crankshaft with the main bearings and pressing it into place using a hydraulic press.
- Reassemble the engine. This will typically involve installing the main bearings, oil pan, timing chain or belt, and any other components that were removed during the disassembly process.
- Verify the engine’s clearances. Once the engine is reassembled, it will be important to verify that all of the clearances are within spec. This will typically involve measuring the clearance between the pistons and cylinder walls, as well as the clearance between the connecting rods and crankshaft.
- Test the engine. Once all of the clearances have been verified, the engine can be tested to ensure that it is running properly. This may involve starting the engine and letting it run for a while to check for any issues.
It is important to note that this is just a general outline, and the specific steps involved may vary depending on the specific engine and the tools and materials that are available.
It is also worth noting that this modification will likely require the services of a machinist or engine builder who has experience with this type of work.
Leave a Reply